What Successful IoT Deployment Looks Like in CMMS and EAM
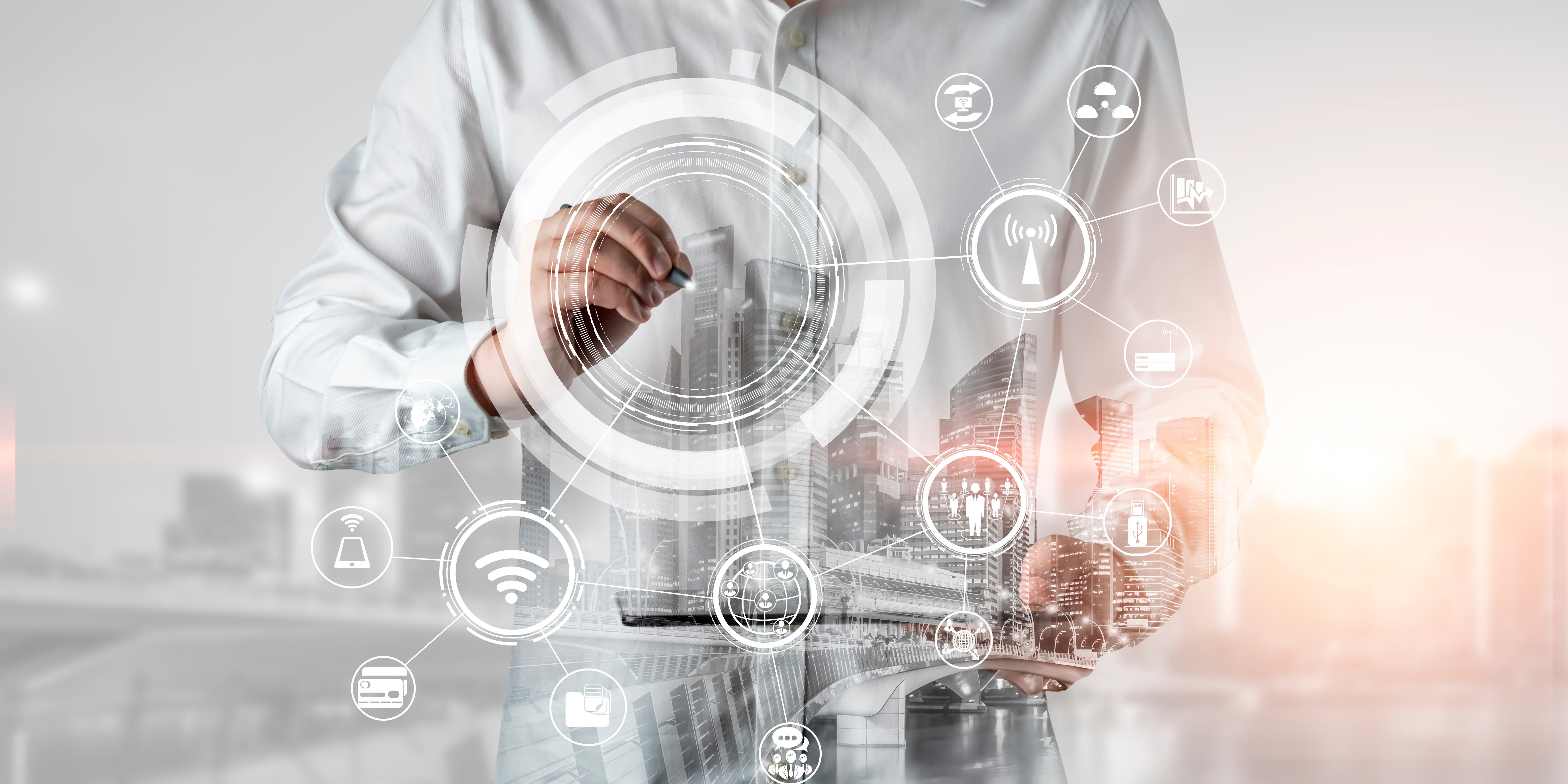
The promise of IoT-enabled maintenance management is compelling: reduced downtime, predictive maintenance capabilities, and optimized asset performance. However, the reality is that many IoT deployments in Computerized Maintenance Management Systems (CMMS) and Enterprise Asset Management (EAM) fall short of expectations. The difference between success and failure often comes down to strategic planning, realistic expectations, and disciplined execution.
The Foundation: Clear Business Objectives
Successful IoT deployments begin with crystal-clear business objectives that go beyond "we want to be more digital." The most successful implementations focus on specific, measurable outcomes such as:
- Reducing unplanned downtime by 25% for critical production equipment
- Extending asset life by 15% through optimized maintenance scheduling
- Decreasing maintenance costs by 20% while improving reliability
- Improving technician productivity by 30% through better work order prioritization
Companies that achieve these results start with a thorough assessment of their current maintenance practices, identifying the highest-impact opportunities where IoT can deliver measurable value. They understand that IoT is not a silver bullet but a tool that amplifies good maintenance practices while exposing poor ones.
Strategic Asset Selection: Quality Over Quantity
The most successful deployments resist the temptation to instrument everything at once. Instead, they focus on strategic asset selection based on criticality, failure impact, and data accessibility. A winning approach typically involves:
Critical Asset Prioritization: Focus on assets where failure results in significant production loss, safety risks, or regulatory compliance issues. These assets justify the investment in IoT sensors and provide the clearest ROI demonstration.
Data-Rich Environments: Start with assets that already generate some maintenance data or have accessible monitoring points. Building on existing infrastructure accelerates deployment and reduces costs.
Scalable Architecture: Design the initial deployment with future expansion in mind, ensuring that sensor networks, communication protocols, and data processing capabilities can grow with the program.
Technology Integration: The Ecosystem Approach
Successful IoT deployments view technology integration as building an ecosystem rather than implementing isolated solutions. This requires careful attention to several key areas:
Sensor Strategy: Deploy a mix of sensor types based on asset requirements - vibration sensors for rotating equipment, temperature sensors for thermal monitoring, and current sensors for electrical systems. The key is selecting sensors that provide actionable data rather than just more data.
Connectivity Solutions: Implement robust, redundant communication networks that can operate in harsh industrial environments. This often means combining WiFi, cellular, and hardwired connections based on location and reliability requirements.
Data Processing Architecture: Build edge computing capabilities that can process sensor data locally, reducing bandwidth requirements and enabling real-time decision making. Cloud-based analytics handle complex modeling and historical trend analysis.
Data Quality and Analytics: From Information to Insight
The most successful deployments recognize that data quality trumps data quantity. They implement rigorous data validation processes and focus on generating actionable insights rather than impressive dashboards.
Baseline Establishment: Before deploying predictive analytics, establish clear baselines for normal operating conditions. This requires several months of data collection and analysis to understand typical variation patterns.
Progressive Analytics: Start with simple threshold-based alerts before moving to complex predictive models. This allows maintenance teams to build confidence in the system while developing the skills needed for advanced analytics.
Continuous Calibration: Implement feedback loops that allow the system to learn from maintenance actions and outcomes, continuously improving prediction accuracy and reducing false positives.
Change Management: The Human Factor
Technology deployment is only half the battle. Successful IoT implementations invest heavily in change management, recognizing that the human element often determines success or failure.
Stakeholder Engagement: Involve maintenance technicians, supervisors, and operators in the planning process. Their field experience provides valuable insights into practical implementation challenges and helps build buy-in for the new system.
Training and Support: Provide comprehensive training that goes beyond system operation to include data interpretation and decision-making processes. Create internal champions who can support their colleagues through the transition.
Workflow Integration: Modify existing maintenance workflows to incorporate IoT data naturally. This might mean updating work order processes, changing inspection schedules, or adjusting maintenance planning procedures.
Performance Measurement and Optimization
Successful deployments establish clear metrics and continuously optimize system performance based on real-world results.
Leading Indicators: Track metrics that predict future performance, such as sensor data quality, alert response times, and maintenance schedule adherence. These indicators help identify issues before they impact operational results.
Lagging Indicators: Monitor traditional maintenance metrics like Mean Time Between Failures (MTBF), maintenance costs per asset, and overall equipment effectiveness (OEE) to validate IoT system impact.
Continuous Improvement: Implement regular review cycles that assess system performance, identify optimization opportunities, and plan for expansion or enhancement.
Common Success Patterns
Analysis of successful IoT deployments reveals several common patterns:
Phased Rollout: Start with a pilot program on 10-20 critical assets, demonstrate value, then scale systematically. This approach allows for learning and refinement while building organizational confidence.
Executive Sponsorship: Secure strong leadership support that can remove barriers, provide resources, and maintain momentum during challenging implementation phases.
Cross-Functional Teams: Form implementation teams that include maintenance, operations, IT, and finance representatives. This ensures all perspectives are considered and organizational silos don't derail the project.
Vendor Partnership: Work with technology vendors who understand industrial environments and can provide ongoing support. The relationship should be viewed as a partnership rather than a transactional purchase.
Measuring Success: Beyond the Technology
Ultimately, successful IoT deployments in CMMS and EAM are measured by their impact on business operations rather than technical specifications. The most successful implementations deliver:
- Operational Reliability: Reduced unplanned downtime and improved asset availability
- Cost Optimization: Lower maintenance costs through better resource allocation and timing
- Safety Improvements: Reduced safety incidents through better equipment monitoring
- Regulatory Compliance: Improved documentation and audit trails for regulatory requirements
Looking Forward: Scaling and Evolution
Successful IoT deployments are never truly finished. They evolve continuously as technology advances and organizational capabilities mature. The most successful organizations view their initial deployment as the foundation for ongoing innovation in maintenance management.
They expand their sensor networks systematically, enhance their analytics capabilities regularly, and integrate new technologies like artificial intelligence and machine learning to further optimize their operations. Most importantly, they maintain focus on business outcomes rather than technology for its own sake.
The path to successful IoT deployment in CMMS and EAM requires careful planning, disciplined execution, and patience for results. However, organizations that follow these principles consistently achieve significant improvements in maintenance effectiveness, operational reliability, and overall business performance. The key is remembering that IoT is not just about sensors and data—it's about transforming how organizations understand and manage their most critical assets.
Topics:
CMMS
Start Your Free Journey to Smarter Maintenance Today!
Take control of your maintenance operations—streamline, schedule, and track all your tasks with powerful maintenance platform. Get started today and boost your team’s efficiency!
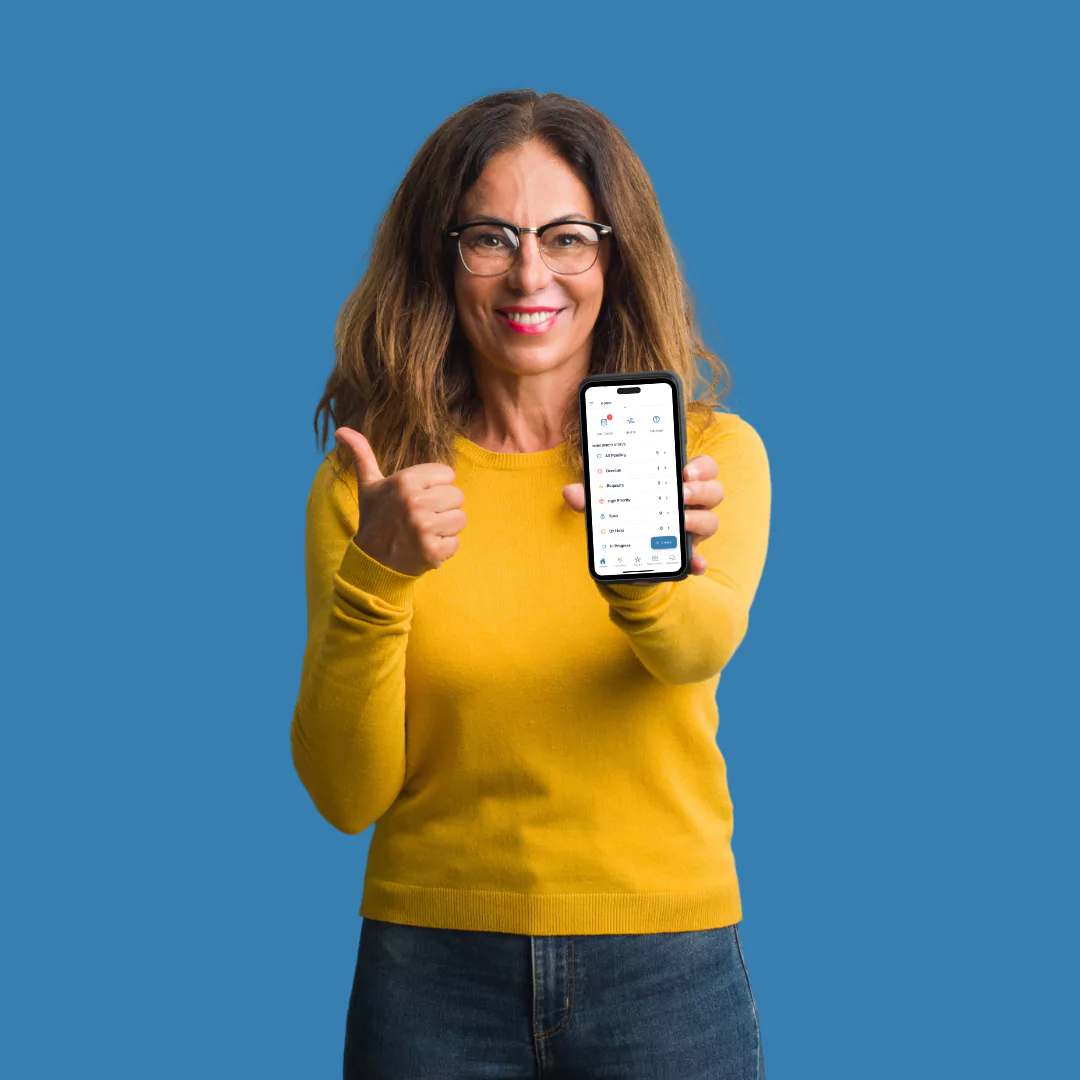